Laser Scanning
Laser scanning offers an efficient, accurate and versatile alternative to traditional survey techniques
At SEP, we are among the leading providers of laser scanning services in the UK.
The application of laser scanning technology has become a recognised and accepted technique in many areas of surveying and civil engineering and is now considered a mainstream surveying method. Although other technologies can provide accurate results for certain applications, laser scanning offers many advantages that have made it the technology of choice for producing high-quality survey datasets in less time.
We have been conducting surveys for over 9 years with a great deal of experience in the planning, analysis and interpretation of measurements taken from laser scans. SEP provides a complete service from data acquisition to data processing to 3D model production. Working in partnership with our clients, we are able to offer the best solution for each project, whether basic surveys or complete 3D reconstructions of entire buildings.
Our head office has all the necessary laser scanners, equipment and software to conduct surveys throughout the UK. Utilising the latest technology and software, we can produce extremely accurate results quickly.
Please contact us for further information about our laser scanning services, or carry on reading to learn more.
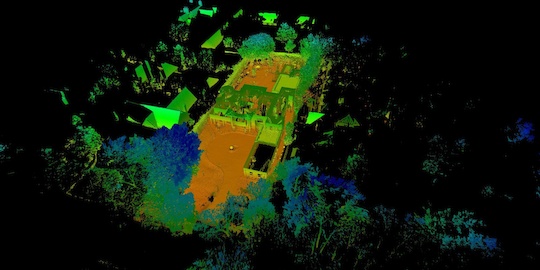
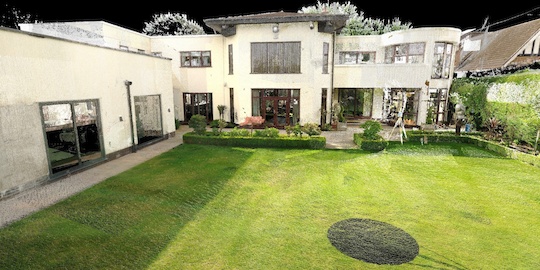
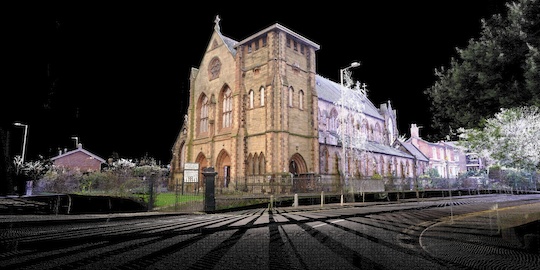
What does 3D laser scanning involve?
The major steps needed to take place when performing a laser scanning survey include:
1. Site Planning and Permissions
The site planning stage is crucial to the success of any laser scanning project. Site visits are an important part of the planning process in order to establish restrictions for access, safety and restricted areas that need to be avoided during laser scanner data acquisition. Typically, permission from the site manager and/or client is required before a survey can be carried out.
2. Safety Procedures and Risk Assessments
Before any data collection can take place, safety procedures must be established and risk assessments performed to ensure that all participants are safe at all times. This includes those conducting the survey as well as those in the vicinity of the work area. Appropriate personal protective equipment (PPE) should be worn at all times during laser scanning activities.
3. Data Acquisition and Quality Control
The point cloud data acquired during a laser scan will determine the quality of the final 3D model which in turn determines how closely it can be modelled on the real-world object or scene it represents. A high degree of accuracy and attention to detail can only be achieved through meticulous planning and careful execution.
4. Data Post-Processing / Data Analysis / 3D Modelling
Once the data has been acquired it must be processed using a suitable software package. The final stage involves creating a fully textured 3D model from the raw point cloud which can then be exported as a mesh or polygon file ready for use in CAD, GIS or other software.
5. Presentation of the final survey results
Once the data has been processed and 3D models produced, it must be presented in a suitable format for interpretation. The final presentation can also incorporate additional survey information, such as levels, digital terrain models (DTM) or contours, and can be used in a variety of applications such as asset management, heritage documentation, damage diagnostics and visualisation.
How does laser scanning work?
Laser scanning is a process that measures the distance from the laser scanner to a target, recording approximately one million measuring points per second to produce a precise, three-dimensional image of its surroundings.
Laser scanning systems allow for automated high-speed data capture of complex surfaces and often in inaccessible environments. The targets can be anything with a geometric form such as buildings, bridges or roads and their surroundings.
What are the benefits of laser scanning?
3d laser scanning offers many benefits, especially for large scale projects, or those located in dangerous or challenging environments.
- Provides a precise, 3D image of the surroundings
- Laser scanning systems can be used on even the most complex structures
- Laser scanner Images can be directly imported into a wide range of software applications
- Imaging in poor lighting and in hazardous areas
- Safe capture of inaccessible areas
- Point clouds for visualisation and measuring
- Accurate datasets are achievable quickly
Laser scanner data outputs
Laser scanners generate a point cloud consisting of millions of data points covering a physical space. There are many possible outputs available from laser scanners, from point clouds and basic measurements through to ortho-images, derived 2D/3D drawings, meshing/surfacing or solid modelling. With suitable plugins, this image can be directly imported into a wide range of software applications.
What is point cloud data?
A point cloud is a set of data points in space describing a physical object. A coloured point cloud format is a computer-based method of storing and processing digital 3D coordinate data from a laser scanner or other 3D sensor such as a structured light device. Point clouds are stored in the computer memory as numerical arrays comprising (x, y) and (z) coordinate data. The term "point cloud" is commonly used to refer to a set of point coordinates that do not lie on the surface of any three-dimensional object.
Point clouds can be displayed as an image for visualisation using either manual or automated computer vision techniques and software.
How detailed is data from laser scanners?
Laser scanning technology provides highly accurate measurements of complex structures that are reliable and can be easily manipulated to create different results for different purposes. The accuracy of a dataset is determined by the number of data points collected and its geometry. Laser scanners have a close-range capability that can be as low as 0.1 millimetres, giving accurate results for short distances. Distances further away from the scanner are increasingly influenced by environmental conditions which can affect the accuracy achieved.
3d laser scanning applications
Laser scanner data can be used and analysed for just about anything. Whether it is architecture, industrial, petrochemical, plant construction, reverse engineering, quality control or historical preservation and forensics – 3D documentation by means of laser scanners offers significant advantages compared with any conventional measuring methods.
Construction and civil engineering:
Laser scanning is widely used in the construction and civil engineering industry to record site information, particularly for large infrastructure projects. Laser scan data can be automatically integrated into a GIS (geographical information system) and added to any other datasets relevant to the project.
Architecture:
Laser scanning can be used to create a 3D model of any designed or built structure. It is also possible to document areas that are difficult to access such as interiors, large structures and complex geometry.
Industry:
In industry, laser scan data is used in various applications for rapid prototyping, manufacturing processes or product development. Laser scan data can be imported into computer-aided design (CAD) programs for further analysis, prototype design or final documentation of the product.
Heritage and cultural heritage:
Laser scanners are used to create 3D models of historical objects, buildings, monuments and artefacts. They are also suitable for use in field recording activities, from sites of natural beauty to World Heritage Sites.
Reverse engineering:
In reverse engineering applications, laser scanners can be used for rapid prototyping or as a basis for computer-aided manufacturing (CAM). The scan data is often imported into CAD programs where it can be manipulated and analysed further.
The benefits of 3D scanning with drones
Much in common with terrestrial laser scanners, UAVs are being used increasingly to provide high-quality data much faster than traditional methods. Combining UAVs with laser scanning technology makes it possible to generate extremely accurate elevation models, digital terrain models (DTM), digital surface models (DSM), point clouds, contour lines and 3D visualisations rapidly.
Laser scanning data captured by drones is becoming an invaluable tool for many organisations, you can learn more about our UAV Drone survey services here.
What are the limitations of 3d laser scanning?
While advances in technology have increased the accuracy and resolution of point clouds, there are still some limitations of laser scanners that should be considered. Ideally, laser scanners should be used on a fine day with no rain. However, most laser scanners are able to collect good quality data even in poor conditions and the results can often be improved by means of filtering and processing.
Get in quote for laser scan surveys
If you're looking to learn more about how SEP can support your project, please contact us.
We provide our clients with tailored solutions for the measurement, inspection and monitoring of assets in a wide range of sectors. We can support you from initial enquiry to delivery, installation and training as well as ongoing maintenance.